Improvement
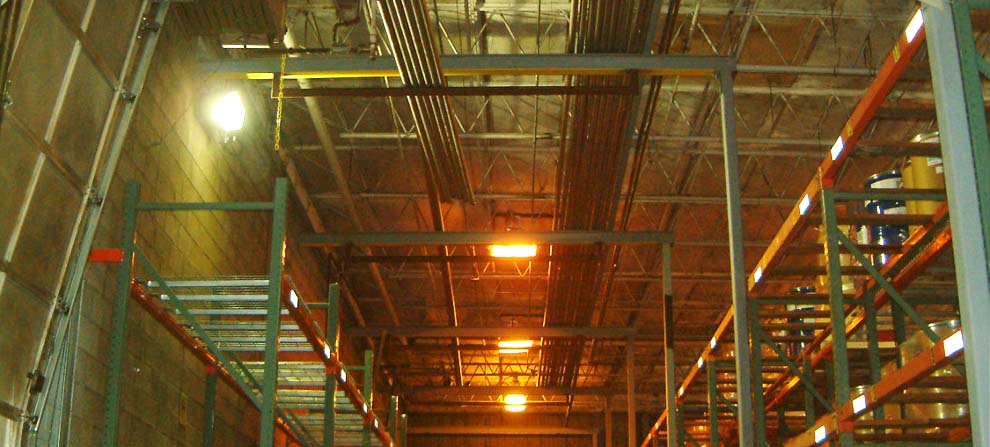
Projects & Maintenance Services of Illinois was incorporated in February of 2008 by husband and wife team Bill and Rose Murry. Bill is certified in welding inspection and is a Certified Plant Maintenance Manager. He has 45 years of welding experience and 33 years plant maintenance experience. PMSI is currently located in Kenosha, Wisconsin at 1346 54th street, at the corner of 13th court and 53rd.
Every mill is unique! Experience from over 8,000 mills worldwide, combined with the market’s most comprehensive offering, means that we can select the optimal mill lining solution for your specific mill.
Performance targets:
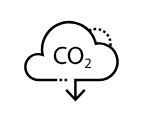
Improved sustainability
Long-lasting, high-performing liners designed with sustainability and safety as top priorities
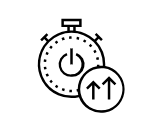
Increased uptime
Shorter and fewer maintenance stops
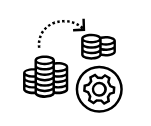
Lower maintenance costs
Reduced cost of operation, quick and easy maintenance
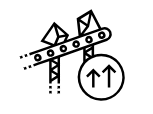
Optimized throughput
Maximized yearly production
Combine for Better Results
Our ability to combine different materials in the same mill, using each material where it performs the best, enables us to optimize your grinding process and make it more sustainable.
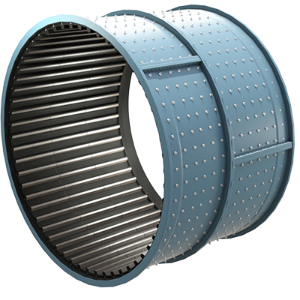
Shell linings
The shell lining has a major influence on grinding efficiency. It transforms the mill rotation into charge motion and both profile and spacing must be carefully selected to suit each specific mill.
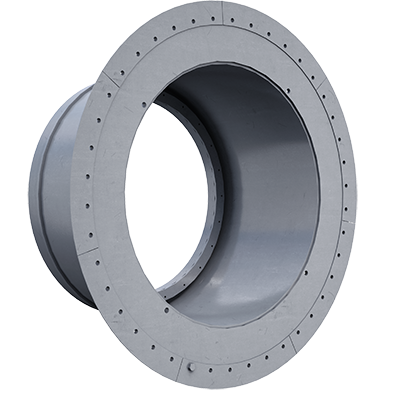
Head linings
As part of a system solution, the head lining is designed with consideration to the shell lining design. All components must be in balance to minimize the number of maintenance stops.
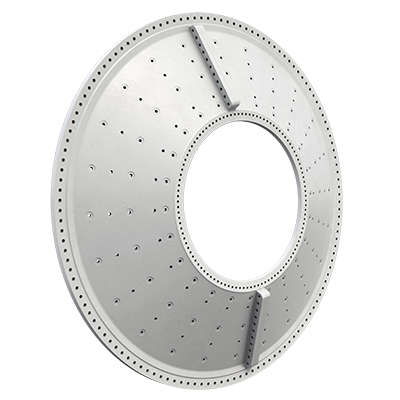
Trunnion linings
Metso trunnion liners are custom-made to protect your mill trunnions from internal wear. Fit is critical, and our trunnion liners can be made to almost any size or shape.
Local support and global expertise
At Metso, cooperation with our customers and availability to offer support and service are of key importance. We have local support close to our customers, several expertise hubs as well as research facilities focused on wear parts development.
Metso’s global laboratory network offers unmatched testing and material development. Our wear parts are manufactured in Metso’s global factory network, utilizing the latest technologies and adhering to stringent quality standards. Today we have nine production units focusing on rubber and Poly-Met wear parts and five foundries for metallic wear parts.
Our unique attachment system, developed for Megaliner mill liners, is an invention which have made a great difference for workers’ safety. Liners are placed by the liner handler operator alone and the bolts are inserted from the outside of the mill.
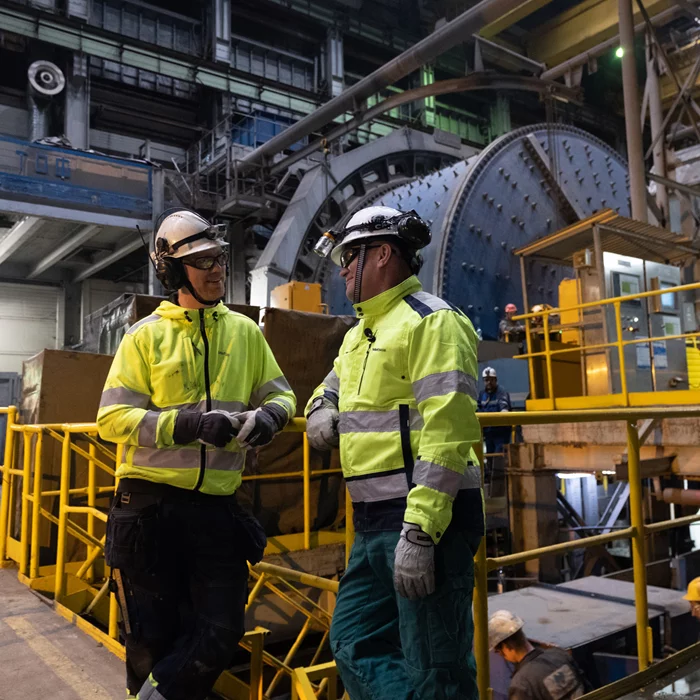
Comprehensive maintenance: A game changer
A leading heavy equipment manufacturer in Pontiac, IL faced staffing issues, maintenance execution problems and rising past-due shipments. To address these challenges, ATS implemented a comprehensive maintenance program, transforming the site into a paragon of operational excellence. As a result, the manufacturer experienced:
- $14.5M year-to-date cost savings
- 27% increase in machine hours
- 100% PM completion rate
- Know all about our project